Statek超小超薄型石英晶体谐振器,下面介绍了一种超微型低轮廓at切割石英晶体谐振器的物理和电学性能及其生产方法的概述。
一,介绍
AT切割石英晶体谐振器在精密频率控制中已经应用了60多年,是目前应用最广泛的晶体类型之一。虽然传统的AT晶体是盘状的,但对较小组件的需求导致了微型AT带的发展。为了满足制造商对更小部件的需求,Statek进口晶振公司开发了一种超微型低轮廓石英晶体,作为其CX-4系列产品的一部分。相比之下,CX-4只需要CX-1的大约三分之一的土地面积和CX-3的大约一半的土地面积。(见表1和图1。)
生产微型石英晶体的一个关键因素是能够产生具有所需的尺寸精度和精确度[1]的谐振器。由于更小的谐振器需要更严格的尺寸公差(例如,为了保持适当的宽长比),所以生产像CX-4这样的超微型谐振器就更加困难了。利用制造石英晶体的光刻工艺和晶片背板,使批量生产超微型石英晶体成为可能。光刻过程提供了所需的精密微加工和尺寸公差,晶片备份器提供了精确的金属沉积到谐振器的电极,用于最终频率调整[2]。
在第二节中,我们概述了用于制造晶体谐振器晶片的光刻工艺。在第三节中,我们讨论了使用晶片背板的最终频率调整。在第四节中,我们简要讨论了谐振器在其封装中的最终组装。最后,在第五节中,我们简要介绍了成品超小型石英晶体谐振器的电学特性。
Statek超小超薄型石英晶体谐振器
二,制造
一个典型的超微型AT空白区约为3.50mm×0.63mm。由于小尺寸石英晶振,获得可接受的产量需要2μm的公差。虽然传统的加工技术不能满足这种严格的公差要求,但光刻工艺能够保持超过1 μm的尺寸公差。
光刻过程从抛光石英晶片(1″×1″或更大)。这些贴片晶振晶片被化学蚀刻到预定的频率,清洗,并使用电子束真空沉积系统用铬和金的薄膜金属化。(也可以使用铝或银等其他金属。)at条图案是使用掩模和双对准器进行光刻摄影生成的,其中晶片的顶部和底部表面同时对齐和曝光。晶体电极和探针垫图案然后由随后的光掩蔽步骤来定义。然后对晶片进行化学金属和石英蚀刻,形成单独的at条。最后,利用孔径掩蔽和薄膜金属沉积[2]将顶部和底部安装垫连接在一起。
一旦光蚀刻过程完成,我们的晶片包含125个单独的超微型AT晶体谐振器,如图2所示。每个谐振器通过两个小石英片物理连接到晶片,它们也将谐振器电连接到晶片上的探针垫。这使得在每个谐振器仍然在晶圆上时对其进行电测试。
三,频率调节
虽然晶圆上的单个谐振器的频率彼此相当接近,但变化可高达1%。这种变化归因于晶片厚度的不均匀性(楔入),以及在较小程度上,金属化厚度的不均匀性。
晶片上谐振器的频率的变化在其生产过程中得到了考虑,因此每个谐振器现在都高于期望的最终频率。然后,使用晶圆备份器,在每个谐振器的电极上沉积一层金薄膜,使其频率降低到最终频率[1]。
晶圆背景器的目的和概念类似于通常的石英晶体谐振器的背镀封装,通过沉积金来控制频率降低。关键的区别在于,在晶圆备份系统中的定位更加精确。由于谐振器已经在封装中,可以应用于背板的精度受到谐振器可以放置在封装中的精度的限制(除非使用图像识别系统)。由于谐振器仍在晶片上,每个谐振器的位置都是固定的和已知的。
此外,尽管在这两种情况下,金通过一系列孔沉积在谐振器电极上,在晶片背板中,暴露谐振器电极的孔本身是石英晶片,使用与石英晶片相同的工艺和使用产生晶片的相同掩模图案制作的贴片晶振。因此,孔径晶片的尺寸和公差为晶片的尺寸,两者的对准度优于25 μm。
由于晶片上每个谐振器在晶片上的位置是固定且已知的,晶片背镀系统可以使用晶片上的探针垫对每个谐振器进行探测,然后自动单独反转每个谐振器
Statek超小超薄型石英晶体谐振器
四,组装
在晶片上的所有谐振器被调整到所需的频率后,每个谐振器被移除并安装在一个陶瓷封装中。该操作使用半自动组装设备进行,该设备从晶圆上冲出并拾取出晶体,同时在晶体封装上分配导电环氧树脂。然后,晶体被定位并放置在晶体封装腔中。(见图。 3.)这个副组装的晶体然后使用匹配的玻璃或陶瓷盖进行密封。
五,电气特性
回想一下,晶体的隔离模式被电地建模为电容C0,与电感L1、电容C1和电阻R1的一系列组合并行。超微型AT晶体与其较大的同类晶体的主要区别在于一个更大的串联电阻R1和一个较小的串联电容C1(两者都是由于电极[3]的面积较小)。在表2中,我们给出了三种不同频率的CX-4 AT晶体的电学参数。使用这些值作为它们较大的CX-1对应物的值(这里没有给出),我们发现R1大约是其较大的CX-1对应物的阻力的2到三倍,而C1大约是CX-1值的一半到三分之一。
在图4中超微型晶体的阻抗扫描中可以看到,这样的小晶体可以很好地表现为电,因为它们的基本模与其他石英晶体的模很好地分离。在大约占晶体基频5%的频带中,只有一种非谐波模式可见。该模态的电阻足够高,而且它离主模态(在频率上)足够远,因此其影响可以忽略不计。
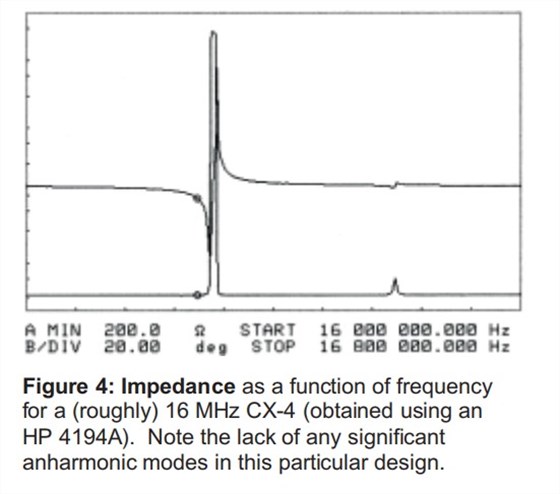